Factors contributing to successful sheet metal fabrication
Release time:2022-12-02 14:51
Currently, Sheet metal manufacturing businesses need to adapt processes to specific jobs while significantly reducing delivery times. Utilizing advanced technologies is a response to this challenge. Let's explore the factors contributing to successful sheet metal manufacturing!
Success Factor 1: Automated warehousing accelerates logistics
Laser cutting shops typically adjust their technology daily to accommodate new jobs. Quick access to sheet metal is a significant advantage. Automated warehouses provide various materials with the click of a button. Intelligent warehouse systems send the required materials directly to the laser cutting system, sort the cut parts, waste, and unused materials, and send them back. Connecting the automated warehouse directly to the machines saves over 70% of the time, leading to faster material supply and higher machine capacity utilization. Automated processing from warehouse to cut parts is achievable in many applications.
Success Factor 2: Deburring machines remove residue
Many suppliers integrate deburring machines into their manufacturing chain to meet the demand for cleanly deburred parts. Machine deburring has proven to be a crucial aspect of sheet metal fabrication. Removing sharp edges from parts reduces the risk of employee injury and simplifies material handling. Furthermore, burrs can cause problems in downstream processing. Burrs and sharp edges from laser cutting can also damage tools and machines in subsequent processing. Therefore, burr-free materials are easier to assemble or mount on welding fixtures.
Success Factor 3: Straightening ensures bending effects
Many laser processing sites don't realize the importance of adjusting flat panels to improve the efficiency of sheet metal fabrication. The more sheet metal is processed, the harder it becomes to correct material defects. Therefore, initially leveling the material is a significant advantage; unlevelled sections of sheet metal during laser cutting can warp and damage the laser head. Additionally, internal stresses after cutting affect the reliability of the bending process when bending sheet metal. Therefore, once the robot starts feeding the panel to the bending machine, operators cannot easily make corrections during the bending process.
Success Factor 4: Successful welding of "stress-free sheets"
Customers will continue to find Sheet metal manufacturing more accurate quality requirements for parts. These include stricter tolerances; sometimes, unlevelled parts may not meet customer tolerance specifications. When welding unlevelled parts to form components, the product may exceed tolerances, requiring significant rework. Bending the sheet metal also causes problems with the time spent on the welding process itself. These problems start with welding preparation; mounting panels on welding fixtures is time-consuming. If the panels bend during welding, problems arise, especially in robotic welding, where deformed workpieces may not be assembled correctly, resulting in unreliable results for the welding robot. Using a straightening machine significantly reduces welding preparation time and greatly improves the reliability of the entire welding process.
Success Factor 5: Pre-leveling reduces milling
In the machinery manufacturing industry, customers have high demands for flatness in the thousandth-of-an-inch range. Therefore, many suppliers integrate grinding or milling machines into their process chain.
Success Factor 6: Intelligent linking of process steps
Sheet metal manufacturing Deburring and leveling can essentially be automated; however, the various processes complicate the supplier's workflow. Therefore, for effective sheet metal processing, the ideal approach is to effectively connect the various equipment components to create a smooth, uninterrupted chain.
Previous Page
Related news
0760-23378116
Address: Shigu Industrial Zone, Wuguishan Town, Zhongshan City
Email:sujiang@zs-jwwj.com
Fax:0760-88202828
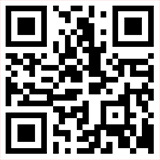