Reasons for deformation of sheet metal parts
Release time:2022-12-07 11:54
Sheet metal parts Reasons for deformation
Common materials for sheet metal parts are construction steel. During the process of cold rolling construction steel into sheet metal, cutting, forming, assembling, and welding to create new sheet metal products, external forces (including machining and lifting) and heating and deformation processing are involved. Some of this deformation is required by the product specifications, while some exceeds the technical standards. This internal stress and deformation exceeding technical standards is referred to as deformation defects. Relevant production process countermeasures should be implemented for prevention.
Analysis of the reasons for deformation deviation of construction steel in the sheet metal manufacturing process. Raw material deformation mainly comes from the rolling process, transportation, and improper stacking of the construction steel. During cold rolling of construction steel, if problems such as uneven heating, bending of hot-rolled strip, and inconsistent gaps in the hot-rolled strip occur, it will cause uneven reduction in the width of the plate. The wider part will be constrained by the narrower part, resulting in compressive stress, while the narrower part will cause tensile stress. Therefore, the wider part may become unbalanced under the compressive stress and cause deformation.
Sheet metal parts Thick steel plates, especially thin metal plates, are prone to partial uneven deformation, wrinkle deformation, or relatively stable wave-like deformation. Larger steel plates are prone to side wave bending, sometimes causing distortion, while larger trough steels are prone to bending, and smaller angle irons are prone to twisting deformation. Construction steel after hot rolling may also undergo deformation during cooling if wet or in humid environments.
What quality standards should sheet metal manufacturing meet?
1. The welding of sheet metal parts should be firm and uniform, without defects such as lack of fusion, cracks, burn-through, gaps, misalignment, etc.
2. Bolts and nuts (columns), bolts and nuts, bolts and nuts (columns), bolts and nuts, etc. After fastening parts, the screw threads should not be deformed (nuts or screws can be freely inserted and removed, and lubrication is smooth without jamming). Riveted parts should be flush with the surface and should not be protruding or recessed (hand magnetic induction lubrication). Riveted parts should be perpendicular to the surface. After riveting, the riveted area should not be deformed. The height and thickness of the pull-over should be uniform, and the top should not have burrs.
3. The dimensions and height of the welded parts of sheet metal parts should not exceed the permitted specifications of the sheet metal parts.
4. The welding length of sheet metal parts is 8-12mm, and the distance between two welds should be 50mm.
5. If the drawings have special requirements for the welding of sheet metal parts, they should be implemented according to the drawings.
6. Sheet metal parts After welding, the surface of the parts should not have defects such as weld beads, pores, weld scars, protrusions, and depressions. Internal defects are not obvious and do not affect assembly. Key components such as doors and panels should also be relieved of residual welding stress to prevent product deformation.
Previous Page
Related news
0760-23378116
Address: Shigu Industrial Zone, Wuguishan Town, Zhongshan City
Email:sujiang@zs-jwwj.com
Fax:0760-88202828
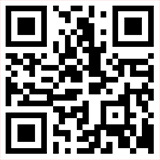