How can sheet metal processing operations reduce processing errors?
Release time:2022-12-26 15:30
Sheet metal processing Precautions for polishing:
Operators of grinding machines must be certified. Unauthorized personnel are prohibited from operating or using grinding machines. Before starting the machine, check the lubrication points of the machine tool and add oil as needed. Check if the grinding wheel, magnetic chuck, and machine operating system are functioning normally.
If the grinding wheel is unsuitable, it should be dressed promptly. When dressing, pay attention to the following: The tip of the diamond dresser must be tangential to the grinding wheel; it must not be perpendicular to the grinding wheel to prevent the grinding wheel from bursting, damaging the diamond dresser, or causing injury. The magnetic chuck must be clean; before each clamping, wipe off dust, iron filings, and other debris from the worktable. To ensure the worktable has sufficient suction for the workpiece, the workpiece must be clamped with a dedicated vise or directly sucked onto the worktable. However, for small and tall workpieces, auxiliary magnets should be added on both sides to prevent the workpiece from flying out during grinding.
When grinding, start the grinding wheel first, then adjust the gap between the grinding wheel and the workpiece. During test grinding, do not cut too much; generally, 2-3 lines for rough grinding and 1 line for fine grinding. Grinding drills larger than size 4 on the grinding wheel is strictly prohibited. When grinding, ensure the grinding wheel cover is properly secured. Opening the grinding wheel cover is strictly prohibited to prevent the grinding wheel from bursting and causing injury. After the machine starts, the operator must not leave the machine. Clean up debris and the area after work. Every step should be carefully taken; sheet metal processing cannot be delayed, as this is related to safety, which is why sheet metal processing is relatively more expensive than other processing methods. This is all reasonable.
Sheet metal processing How to operate to reduce processing errors?
Many processed materials, or CNC processed materials, now have high requirements in terms of precision, with specific work requirements. Errors lead to material and technical waste. It necessitates material replacement. Now I understand why work errors are bad!
For the sheet metal processing industry, drawings are like the commander of a ceremonial guard; without a commander's instructions, the result will be a mess. Therefore, before sheet metal processing, it is imperative to check if the drawings are complete, including the front, side, and back views, as well as the marked dimensions. If you don't check these materials and only discover incomplete drawings (missing back, side, or front views or unmarked dimensions) during actual processing, it will result in inaccurate workpiece processing, or even delays, affecting production efficiency.
From the above analysis, we should understand why it is necessary to Sheet metal processing check the completeness of the drawings beforehand. With the improvement of people's living standards, the requirements for the precision and quality of sheet metal processing are also constantly improving. Pay attention to several areas that are prone to errors.
1. First, pay attention to areas with larger dimensions. Enlarging the drawings during processing ensures the accuracy of the processing parameters.
2. Second, when encountering special angles, it is necessary to carefully check and, if possible, fold to ensure accuracy before proceeding with processing.
3. Then, highlight areas prone to errors. For example, some edges may appear symmetrical visually, but are only similar in reality. In such cases, key markings can enhance focus during the processing.
Previous Page
Previous Page
Related news
0760-23378116
Address: Shigu Industrial Zone, Wuguishan Town, Zhongshan City
Email:sujiang@zs-jwwj.com
Fax:0760-88202828
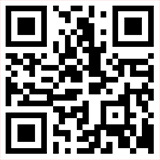